The development speed of SiC in recent years has almost exceeded everyone‘s expectations. In recent years, with the efforts of various SiC manufacturers, SiC MOSFET devices have made significant improvements, and manufacturing methods and defect screening have also made certain progress. The commercialization and transportation of SiC have significantly accelerated.http://www.ic-bom.com/
There have always been two different types of structures, planar gate and groove gate, in the debate over the technical route of SiC MOSFETs. The so-called trench grating can be easily understood as "digging a pit" on a flat foundation (as can be clearly seen in the comparison of the schematic diagram in the following figure). International SiC manufacturers are using trench grids to maximize the potential of SiC. Looking at it, some manufacturers are digging one pit, some are digging two pits, and some are digging diagonally. Various technical structures are emerging one after another, and there are also many highlights.
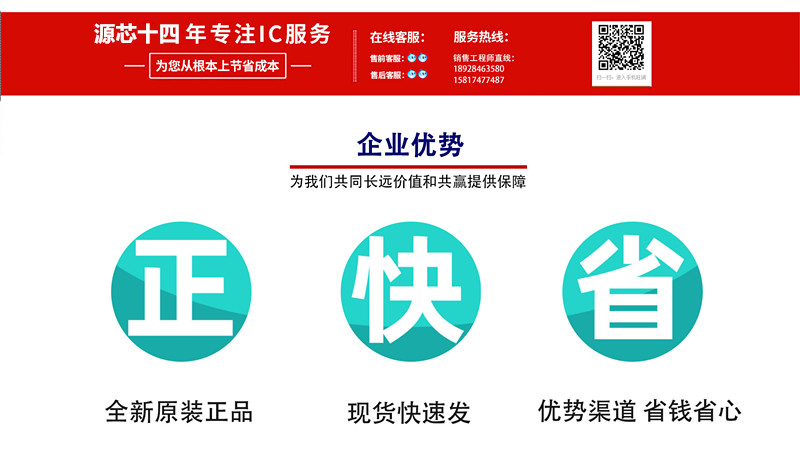
Before discussing SiC MOSFETs, let‘s first review the development history of silicon based MOSFETs. In the 1970s and 1980s, most silicon MOSFETs used for high-power use were vertical conductive paths and planar gate structures. By the 1990s, silicon MOSFETs began to use "trench digging" to improve efficiency. Nowadays, the use of groove structures in SiC MOSFETs has attracted much attention due to its ability to reduce conduction resistance. So, should SiC MOSFETs choose planar gate or trench gate?http://www.ic-bom.com/
The planar gate structure is the earliest, most widely used, and most reliable architecture in the industry. The planar SiC MOSFET was commercialized in 2011, with CMF20120D introduced by Cree at the time. The planar gate structure still dominates today due to its advantages such as simple structure, easy manufacturing, and reliability. However, driven by reducing chip size and thus increasing production capacity, its horizontal topology limits the extent to which it can ultimately shrink.
Grooved gate structure is an improved technique that refers to the formation of MOSFET gates on the sidewalls of grooves formed on the chip surface. The characteristic resistance of groove gate is smaller than that of plane gate. Compared with plane gate, groove gate MOSFET eliminates the JFET region, so there is no JFET resistance and one less resistance. One of the purposes of turning to trench gate is to achieve a lower specific on-resistance (Ronsp, resistance x area), which allows chip manufacturers to reduce the size of bare chips, use fewer SiC raw materials, and thus increase production.
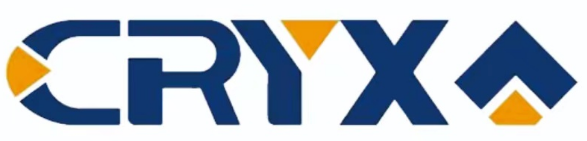
In theory, groove gates can greatly improve device parameters, reliability, and lifespan. But its difficulties are also very obvious. It is difficult for groove MOSFETs to achieve reliable and stable operation. The design of the trench gate must address the problem of maximizing the high electric field (greater than 9 times Si) of the SiC at the top of the device, while protecting the precision gate oxide located at the same top of the device from the influence of the same electric field. This balancing behavior requires clever and complex device layout, otherwise the drift zone will require severe derating, thereby eroding the gain of the trench architecture. Therefore, one drawback of grooved MOSFETs is that their design is more complex, usually requiring more manufacturing steps and requiring higher process complexity. And there are also certain risks in terms of reliability.http://www.ic-bom.com/
To this end, SiC chip suppliers, especially international manufacturers, are leveraging their respective capabilities to explore SiC groove MOSFETs.
From the actions of various manufacturers, it seems that the device structure of SiC MOSFETs is returning to the path of IGBT, and moving towards groove type is the only way for SiC MOSFETs. Most domestic SiC MOSFET manufacturers mainly rely on planar gates. Currently, planar SiC MOSFETs are still the mainstream and the main development path for domestic manufacturers.
As John Palmour, co-founder of Wolfspeed, stated in an interview article published by German media Elektroniknet, he believes that the technological advantages of planar gate SiC MOSFETs are far from exhausted.
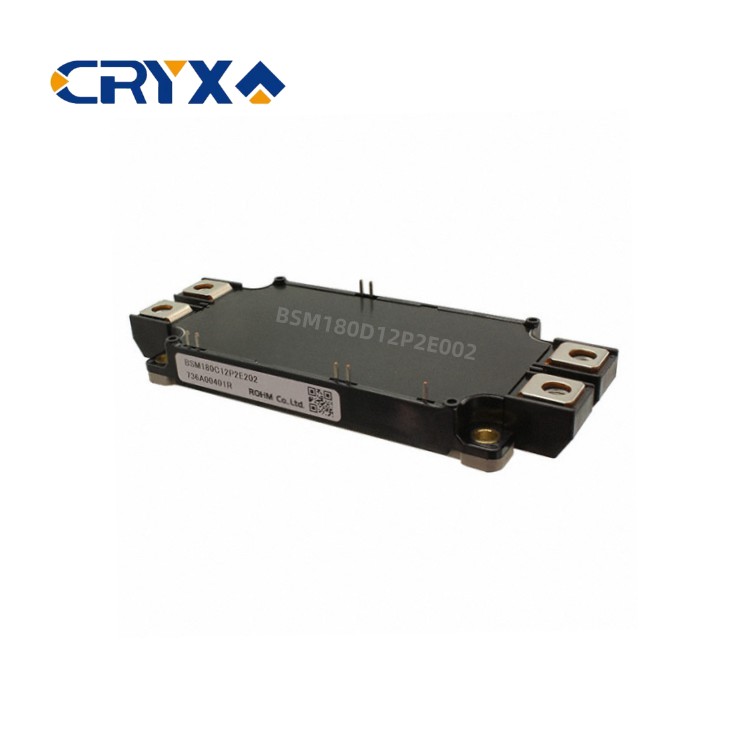
SiC MOSFET supplier Painjie is one of the pioneers in the domestic SiC field. Previously, Dr. Huang Xing, the founder of Painjie, also mentioned that SiC materials are different from silicon based materials. Due to the excellent performance of silicon carbide, laser etching can infinitely reduce the pitch, thereby achieving better HDFM efficiency. Therefore, there is no need to dig grooves like silicon-based chips to shrink the pitch. In the coming years, planar MOSFET technology will still be the mainstream of automotive silicon carbide MOSFETs. Based on a planar gate structure, Painjie has released SiC MOSFETs for various voltage platforms between 650V and 1700V, and has successfully supplied them in bulk to leading new energy enterprises, achieving "on board".http://www.ic-bom.com/
It is not yet clear when domestic SiC manufacturers will "dig trenches" in the future. But even if we want to move towards groove gate structures, it is not easy for domestic manufacturers. As mentioned earlier, the design of groove gates is extremely difficult, and there are also high requirements for manufacturing processes. International large factories often adopt the IDM model, which allows for continuous experimentation between manufacturing and their own design. Domestic manufacturers generally use FablessMOS, and it may take some time to step into the groove type.
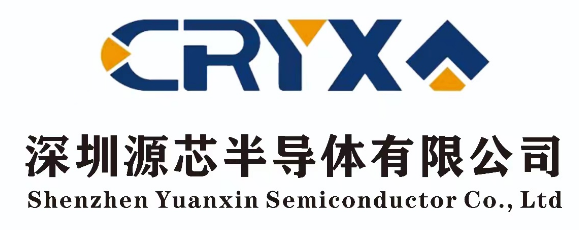
In addition, the high patent barriers of groove structures are also obstacles that domestic manufacturers need to overcome. International SiC giants have been laying out in the SiC MOSFET field for many years and have also accumulated many patents. Therefore, veteran SiC manufacturers holding key patents are expected to gain a long-term competitive advantage in the market. The following figure shows the situation of SiC patent holders according to Yole‘s statistics. Although many companies are focusing on establishing vertically integrated supply chains to ensure the long-term development of their SiC business, few companies have developed a strong patent portfolio throughout the entire SiC value chain, and domestic SiC manufacturers still have great room for development.http://www.ic-bom.com/
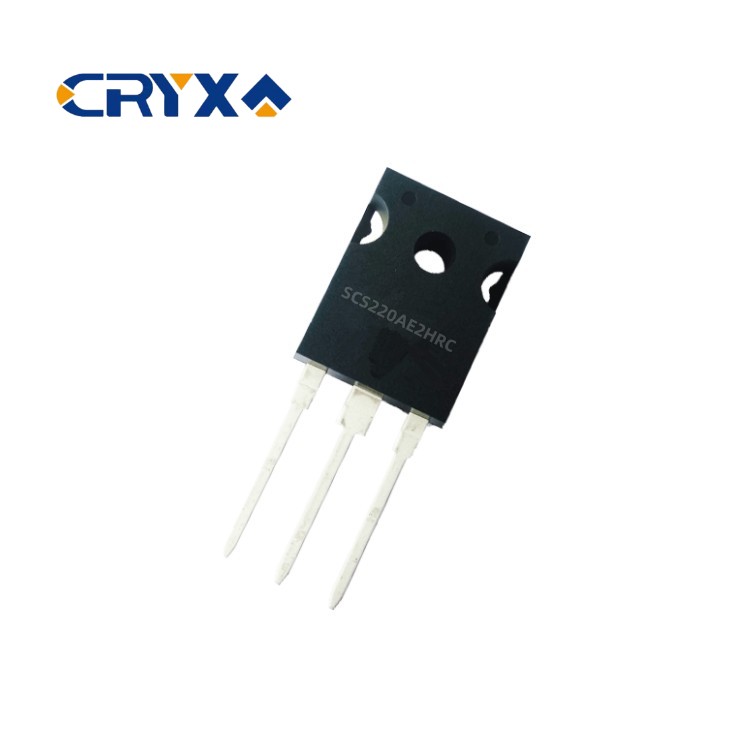