Although digital and emerging M&A activities often indicate an increasing interest in this composite material, only by finding solutions to the three main obstacles currently hindering the wider adoption of
SiC can its expected position in the power electronics field be determined.http://www.ic-bom.com/
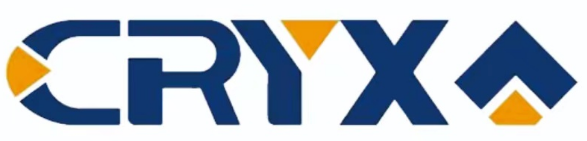
1、 Cost
So far, the cost of SiC modules cannot provide the possibility of popularizing this technology in electric vehicles other than high-end ones. For the same reason, the industrial sector, which targets 3300 V for its high-power applications, is still unwilling to venture into SiC and still relies on the Si IGBT option. According to Yole SystemPlus analysis, the cost of substrate manufacturing and epitaxial stages accounts for 59% of the total wafer cost (average cost of 1200 V SiC MOSFETs), followed by yield loss in front-end processes (24%). In terms of bare chip ampere cost level, Wolfspeed and ROHM Semiconductor performed the best, confirming the clear advantage of controlling the entire supply chain in competition. In order to reduce costs, several scenarios are being considered. By Wolfspeed, II-IV Incorporated, and now Coherent, while SiCrystal is in progress. However, quality issues are still delaying actual start-up, and it is now expected to be in 2025. The emerging technology engineering SiC substrates compatible with Si production lines, as well as wafer process innovation, are also being developed.
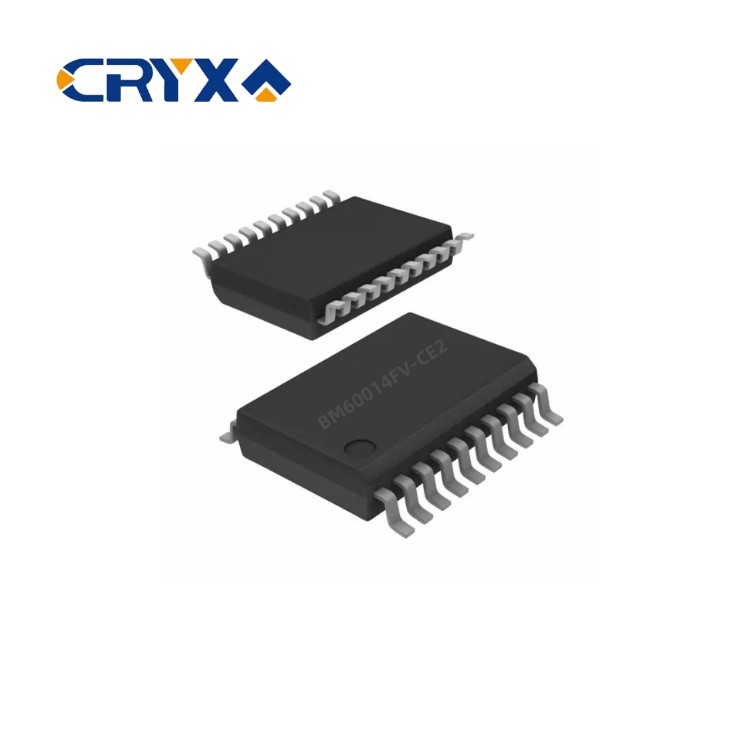
2、 Reliability
Although integrated into commercial automotive systems (Tesla and Lucid Air inverters/Toyota Mirai II boost converters), there is insufficient evidence to prove the long-term reliability of SiC products. This is another argument that has led the industrial sector to adopt a wait-and-see attitude.http://www.ic-bom.com/
3、 Packaging
To fully benefit from the advantages of SiC technology, it is necessary to find suitable packaging solutions. The problem lies here: although there are multiple validated options in the case of Si IGBT, the packaging options for SiC MOSFETs are still in their early stages and only a few designs developed by Denso, Wolfspeed, and ST Microelectronics have been demonstrated. These designs include high-temperature compatible and low loss materials, whether on the substrate (materials with good heat dissipation performance, such as AlN and AMB-Si3N4), packaging (high-temperature epoxy resin or silicon gel), chip attachment (such as silver sintering) or interconnection (with low inductance interconnection, such as top Cu lead frame). There is still a lot of work to be done before providing standardized solutions.
On February 1st, Wolfspeed and ZF announced the establishment of a strategic partnership with the goal of developing future silicon carbide semiconductor systems and equipment for mobile, industrial, and energy applications. One way to achieve this goal is to establish significant SiC production capacity in Europe.
Wolfspeed‘s new factory in Germany will become the world‘s largest 8-inch dedicated SiC device factory and the only factory in Europe capable of producing 8-inch SiC wafers in large quantities (excluding some SiC compatible capacity of STMicroelectronics). This move will consolidate Wolfspeed‘s leadership position in the SiC wafer field, while also targeting the SiC device market currently dominated by European companies.http://www.ic-bom.com/
Wolfspeed is the only company in the world that can mass produce 8-inch SiC wafers through its existing wafer factory located in New York, USA. This dominant position will continue for the next two to three years until more companies start building production capacity - the earliest being the 8-inch SiC factory that Italian Semiconductor will open in Italy in 2024-5.http://www.ic-bom.com/
The United States is leading in the SiC wafer field, with Wolfspeed working with Coherent (II-VI), onsemi, and SK Siltron css, which are currently expanding their SiC wafer production facility in Michigan. On the other hand, Europe is in a leading position in SiC devices.
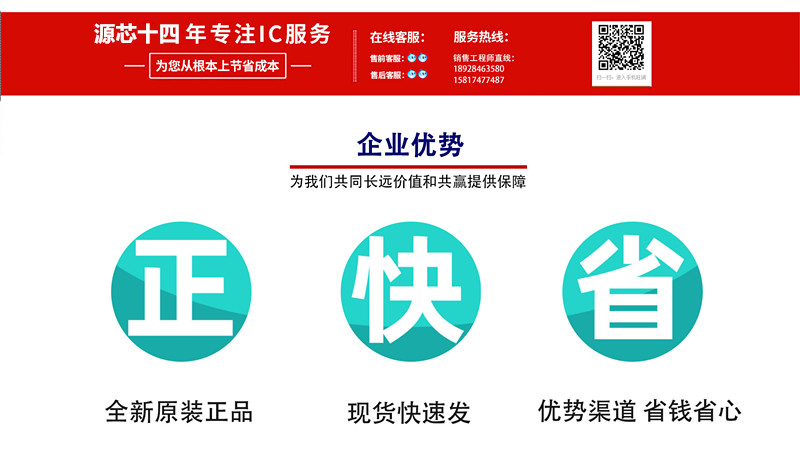